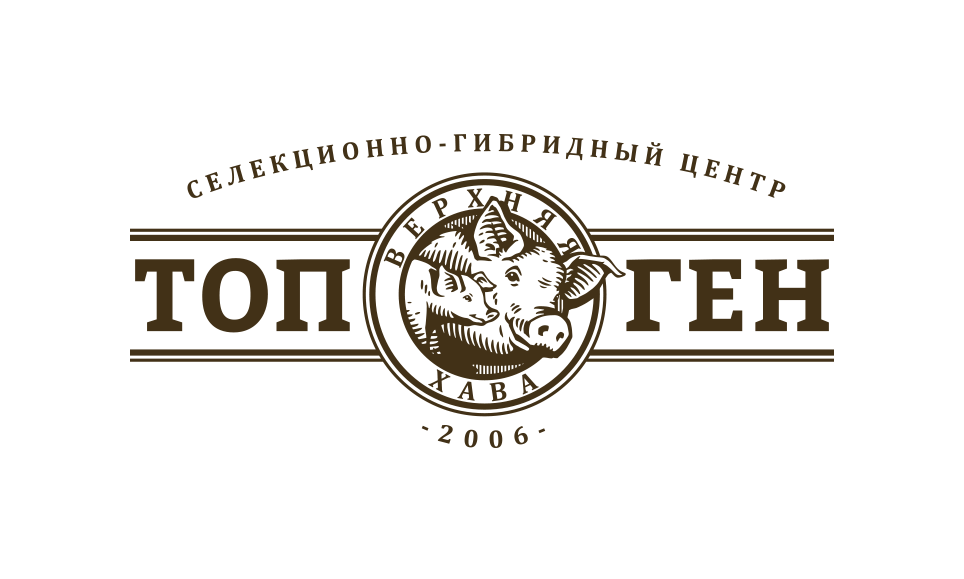
Специалисты знают, что в структуре стоимости конечной продукции животноводства наибольший удельный вес имеют затраты, связанные с производством или покупкой кормов. В свиноводстве сложно уменьшить расходы на ветеринарную обработку поголовья, закупку электроэнергии и газа и др. Однако есть категории, которыми можно и нужно управлять. В их число входит конверсия корма. Системный подход к кормлению — главное условие повышения конкурентоспособности продукции, а значит, рентабельности предприятия. В Верхней Хаве Воронежской области построен и выведен на проектную мощность комбикормовый завод.
Основная задача, стоящая перед коллективом ООО «Селекционно-гибридный центр» ТопГен, — производство племенных свиней высочайшего качества. Это позволяет значительно снизить зависимость российских свиноводческих предприятий от зарубежных генетических компаний. Однако свиней современных пород и линий недостаточно просто хорошо кормить, чтобы получить желаемый результат.
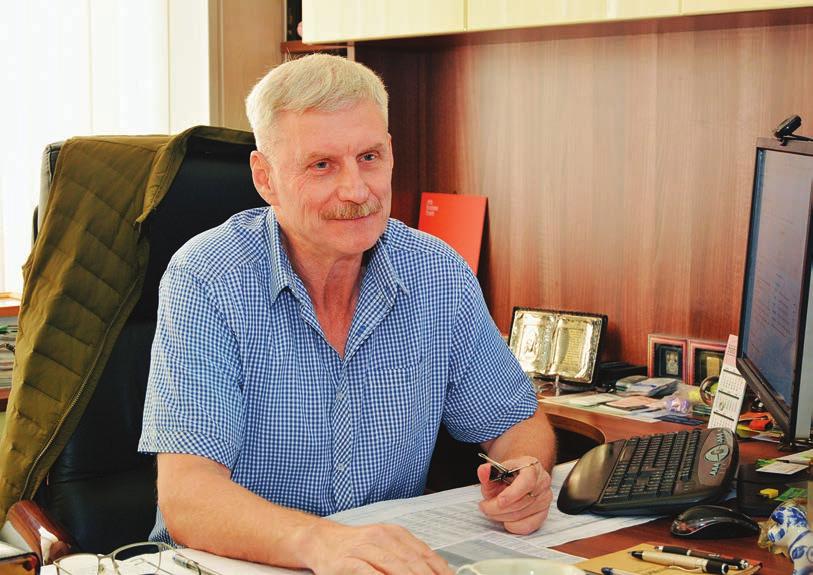
В промышленном птицеводстве средняя конверсия корма составляет 1,6, в промышленном свиноводстве производство свинины считается рентабельным, если конверсия корма варьирует от 2,5 до 2,7. В СГЦ конверсия корма при выращивании племенных хряков составляет 2 и ниже.
— Снижение конверсии корма — не самоцель: в погоне за такими показателями можно потерять качество мяса. Наша задача — получить вкусную свинину при минимальных затратах, — говорит руководитель. — Мы занимаемся селекционной работой течение 15 лет, последние пять из которых — с использованием методов геномной селекции.
Поэтому наши хряки обладают качествами, которых нет у аналогов на других предприятиях. Самое главное — животные здоровы, а значит, могут полностью реализовать свой генетический потенциал.
В СГЦ ежегодно тестируют 12 тыс. хряков отцовских (терминальных) линий. Именно они передают мясные качества потомству в системе трехпородной гибридизации. На станцию контрольного откорма (сегодня на предприятии 191 оборудованная веб-камерами станция, в планах увеличить их количество до 500) поступают чипированные хрячки живой массой от 30 кг. Аппарат в автоматическом режиме определяет предназначенное для конкретного животного количество корма с точностью взвешивания 2 г, фиксирует число подходов к кормушке в течение дня, время, затраченное на прием корма. Потом все это соотносят с приростами живой массы, содержанием внутри мышечного жира и другими показателями. На основе этих и других данных специалисты определяют эффективность использования корма и корректируют рецепты комбикормов. Их производят сами.
— До недавнего времени в СГЦ работал комбикормовый завод мощностью 250 т в сутки, — продолжил Антон Геннадьевич. — Качественный продукт круглосуточно производили на старом советском оборудовании и достигли больших успехов. Поголовье свиней ежегодно увеличивалось, следовательно, росла потребность в корме. Решение построить новый комбикормовый завод мощностью 500 т в сутки было неслучайным. Данных о конверсии корма, получаемого на новом заводе, пока нет (результаты будут известны после того, как животных снимут с откорма в 5,5 месяца). Совершенно определенно можно говорить о том, что конверсия корма, произведенного на новом заводе, окажется не хуже, чем конверсия корма, полученного на прежнем.
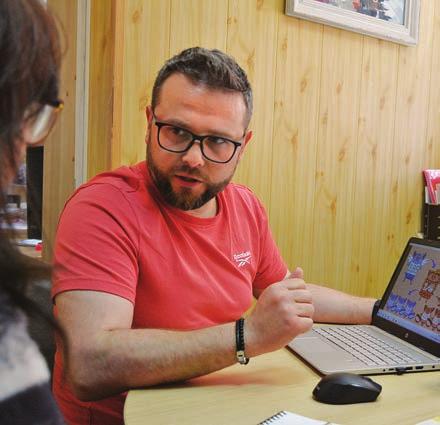
Нередко в торговую сеть поступает мясо с небольшими прожилками жира (либо без них) между мышечными волокнами. Такое мясо сухое и невкусное. Производителей колбас это сырье вполне устраивает, но у потребителей большим спросом пользуется мраморная свинина. Значит, нужно убрать слой хребтового жира и увеличить количество внутримышечного. В этом главная роль принадлежит селекционерам СГЦ и специалистам по кормлению.
На предприятии рецепты комбикормов разработали именно для своего по головья свиней и на конкретный период (пять лет назад рецепты были другими, а еще через пять лет они будут отличаться от нынешних). Учитывают и то, что у чистопородных особей и животных разных линий отзывчивость на один и тот же корм не одинакова. Например, у двух хряков, полученных от одних родителей, характеризующихся одинаковой скоростью роста и имеющих одинаковый селекционный индекс, разность между конверсией корма может составлять 0,5.
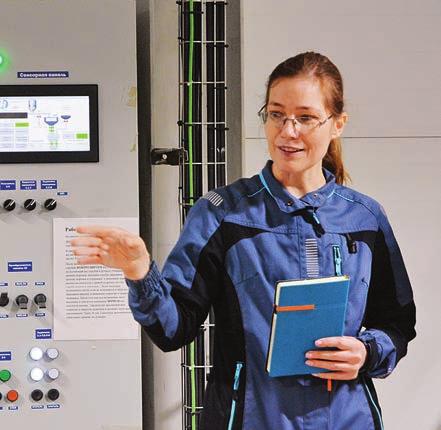
Растительное сырье — собственное, аминокислоты, витамины, источники белка и другие необходимые ингредиенты — покупные. На складе создан стратегический запас всех компонентов, что обеспечивает бесперебойное производство комбикорма.
Согласно проекту технологическое оборудование разместили на каждом этаже девятиэтажного здания (если бы цехи располагались горизонтально, их протяженность составила бы несколько километров). Сначала посетили цех приготовления премиксов на первом этаже. Процесс их производства практически полностью автоматизирован, компоненты на полках расположены так, чтобы их удобно было доставлять к рабочему месту. Оператор получает распечатанный на принтере рецепт. Состав премикса сложный: он включает в себя 43–44 компонента. Дозирование требует особой точности, поэтому аминокислоты, витамины, органические микроэлементы и другие ингредиенты взвешивают вручную. Ошибки недопустимы. Измельченные в дробилке отруби смешивают с микро- и средними компонентами в смесителе. Полученный продукт фасуют в мешки, отправляют на грузовом лифте на верхний этаж и загружают в бункеры. Оттуда премиксы поступают в цех по производству комбикормов.
— Мы постоянно мониторим рынок витаминов, ферментов, подкислителей, — говорит Наталья Марковна. — Их использование позволяет улучшить конверсию корма. Показатели, полученные при скармливании комбикормов племенным и товарным свиньям в СГЦ, фиксируем и анализируем. На заводе выпускаем комбикорма и премиксы разных марок для животных всех половозрастных групп. При этом строгособлюдем требования стандартов.
На верхнем этаже установлен очиститель. В него при помощи нории с находящегося поблизости элеватора подается зерно. Его перемещают в огромный бункер. Туда же добавляют шроты, микро- и другие компоненты — премиксы, соль поваренную, сахар и бензойную кислоту. Потом сырье попадает на промышленные весы, рассчитанные на 2500 кг (минимальный предел взвешивания — 20 кг, дискретность — 1,8 кг) навтором этаже.
На шестом этаже размещены бункеры для зерна пшеницы, ячменя, овса, кукурузы, а также для белковых компонентов комбикорма — соевого и подсолнечного шротов. Предусмотрены бункеры для такого сырья, как горох, тритикале и рапсовый шрот. Их планируют использовать в дальнейшем. Зерно поступает в дробилку на пятом этаже. Мощность этого оборудования — 20 т в час. Измельченное зерно подается в бункеры, расположенные над пресс-грануляторами.
Термическая обработка — обязательный процесс. Такой прием дает возможность обеззаразить корм, повысить его биобезопасность и тем самым предотвратить занос вируса африканской чумы свиней и других заболеваний. На двух линиях гранулирования применяют прессы производительностью 10 т/ч каждый. Сыворотка подается в смеситель из отдельного бункера. За счет этого повышается технологичность процесса. Из четырех бункеров вместимостью 20 т каждый на гранулирование одновременно может поступать сырье для приготовления рассыпных комбикормов по восьми рецептам. Очередность их производства определяют операторы.
От профессионализма специалистов зависит качество получаемого продукта. Пульт управления находится здесь же. Он оборудован видеокамерами и компьютерами. На мониторах — схематическое изображение оборудования и операций, которые выполняются в автоматическом режиме. Если происходит сбой, оператор дает команду механикам устранить неполадки. Рядом с пилотами (так на предприятии называют операторов) работают технологи по комбикормам, которые составляют рецепты. В СГЦ планируют создать лабораторию, где будут определять качество сырья методом мокрой химии.
На выходе из пресса (он установлен на третьем этаже) температура массы достигает 80 °С. Полученные гранулы охлаждают (продукт поступает из главного смесителя в охладитель) и рушат (измельчают). Эта операция выполняется при помощи рушалки (вальцовая мельница), которая превращает гранулы в крупку.
Мы проследовали на второй этаж в зону погрузки, где в специализированный автотранспорт из силосов объемом 22,5 т по рукаву поступает готовый комбикорм. Его взвешивают автоматически, так как процесс отгрузки полностью компьютеризирован. Бункеры не заполняют новым комбикормом, пока не отгрузят предыдущие партии. Такая технология позволяет исключить накопление остатков мелкой фракции и не допустить ее контаминации, а также вести учет продукции. С завода корм бесперебойно доставляют на все площадки СГЦ.
Технике безопасности на предприятии уделяют особое внимание. На каждом этаже перед входом в цех на стене висят стенды с фотографиями оборудования. Алгоритм его обслуживания прописан досконально. Очередность операций обозначена красными стрелочками. Такая схема — не окончательный вариант: изменения в нее вносят постоянно для того, чтобы оптимизировать процесс. Уборку производственных помещений также проводят в соответствии со стандартами, установленными на предприятии.
В цех можно попасть только через санпропускник. Есть душевые и комнаты для приема пищи (персонал не покидает помещение до конца смены). На входе расположены коврики с дезраствором, на стенах — санитайзеры. Для кормовозов оборудована весовая, машины следуют по отдельному маршруту и не пересекаются с транспортом, который привозит сырье из разных регионов страны. На заводе функционирует мощная газовая котельная: на современных установках вырабатывается пар и подается на пресс-грануляторы. Этот процесс также идет без участия человека.
Рядом находится старый комбикормовый завод. Это скорее цех, если сравнивать его с новым предприятием. Здесь многие операции выполняли вручную, но несмотря на это, на протяжении многих лет получали по 240 т в сутки качественного комбикорма и полностью обеспечивали им животных на свинокомплексе.
— Первый комбикормовый завод мощностью 10 т/ч был построен в 2007 г. На технологических линиях выполняли сепарирование, шелушение пленчатых культур, измельчение сырья, микро- и макродозирование, смешивание, ввод жидких компонентов (например, масла) и гранулирование. Сегодня помещение используем как склад, — прокомментировала Наталья Марковна.
Еще один пример для наглядности: один хряк за жизненный цикл оплодотворяет 1,5 тыс. свиноматок. Из расчета на опорос производители получают 1,5 т свинины. Перемножаем показатели: число свиноматок — 1,5 тыс., количество мяса за опорос — 1,5 т, конверсия корма — 2,7 (среднее значение во многих отечественных хозяйствах), генетическое влияние хряка — 0,5, цена 1 кг комбикорма — 26 руб., снижение конверсии корма на 0,1. Итог — почти 8 млн руб.: сумма, которую можно сэкономить либо потерять в случае изменения конверсии корма лишь на 0,1. Вот почему так важно учитывать этот показатель. Разумеется, качество комбикорма должно соответствовать стандартам СГЦ. Рецепты комбикормов получают все клиенты, приобретающие животных в Верхней Хаве.
Работать на современном предприятии нелегко: все процессы автоматизированы и стандартизированы, требования нужно выполнять неукоснительно. Но коллектив имеет богатый опыт, накопленный при эксплуатации прежнего комбикормового завода (именно тогда был сформирован системный подход к организации производственного процесса), а также знания, которые все успешно применяют на новой площадке.
Ввод в эксплуатацию такого мощного завода, безусловно, даст дополнительный импульс СГЦ ТопГен для динамичного развития, дальнейшего внедрения прогрессивных технологий и уверенного движения вперед в любых экономических условиях.